Ribbon Dancer
project scrapbook:
Early on, I had to quickly (and cheaply) come up with
slip rings for the phi axis. This allowed testing of unlimited freedom
to move in both axes-- a very nice addition.
(more on slip rings)
After receiving word that I was awarded the SCI project,
I started serious thinking about the choice of hardware. Although I
had demonstrated the feasibility of an open loop system, it was clear
to me that a large robot, operating in a public space should be closed
loop, to detect any "problems" (although none should ever
occur :)
Once the decision to close the loop is made, the jump
from steppers to servos is not a large one, in terms of expense. Having
developed a certain fondness for Compumotor over the years (I have used
steppers and drives from them that are over 20 years old, and NEVER
seen them fail; plus they have a great web site and document
their old products), I approached a local distributor for advice
and pricing. The people at Braas.
Co. were very helpful, and after some discussion about ways to approach
my application (which I think surprised them), they lent me a 6K4 controller,
with one Gemini drive and one size 23 servo with an 8:1 gearhead. I
found a reasonably priced used TQ10 drive and motor at D&S,
and quickly got both motors running by sending hi-level commands in
6K language over Ethernet:
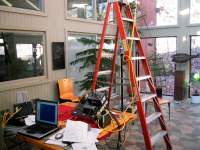
Unfortunately, I thought my early ease getting things
to work would mean that I would have no trouble streaming my dance paths
to the motors. Wrong. Although the 6K is easy to use, it became clear
after many hours of trying various methods, that it was not designed
to produce multiaxis smooth contours in the way I desired--
arbitrary length, and the ability to repeat a contour without any "seam"
(velocity = 0). I learned a whole lot, as this was my first experience
using servos-- but mostly, I learned that the 6K controller is not what
I'm looking for.
On the other hand, I did some testing of the servo motor's
capabilities (there was some concern from the Parker engineering staff
that I might have trouble tuning the servos in such a high compliance
system). I was blown away by their performance:
Video clip of 4 revs/sec (wmv).
I fixtured a 92 oz-in motor with 8:1 gearhead, and attached
a 6' graphite rod. I then tuned the motor without much difficulty. I
then commanded 10 revs, v=1rps, a=10rpsps. No sweat. I increased the
v to 2, then 4rps-- holy crap! I chickened out after 8 rps, which was
truly frightening-- I later calculated the speed at the rod's tip: over
200 mph. I will not soon forget the sound it made slicing through
the air. I'm not sure how much faster it could have gone before losing
position.
I'm now trying to decide upon the fundamental question
of how to "best" send my dance paths to the servo drives.
Since I already have step/direction software written, that is an intriguing
possibility...