"Divergentes"
-- a month-long residency, making CNC sculpture in the Basque region
of Spain. I haven't had time yet to add and condense. But for now, just
time for some pictures of the final sculpture:
The uncondensed project blog:
May 20-- It's time to say goodbye to "the boys" at Robotiker.
Alfredo and Juanma have been a tremendous help-- I will miss them!
All the pieces are cut and separated. Now it's time to head to
Inasmet, in San Sebastian.
There I will weld and bend the sculpture into its final form.
Some crude renderings of the idea-- there will be many more levels of bending.
May 17,18,19-- lots and lots of cutting.
6mm of stainless cut with 2000 watts and high pressure nitrogen.
Very expensive zinc-selenium lens focuses the laser beam. It needs
periodic cleaning and great care.
Going through *lots* of N2!
Anton (one of the other Divergentes artists) is making a video documentary of
all the projects. He stops by and gets some footage...
... and accompanies us to a great place for lunch.
The last cut-- "Ahhhhhh."
It's been an amazing journey. We pushed the laser to its limits (not at all designed
to do what we did). There were many, many technical problems, and several times it looked as though we had hit a dead end. But
with every problem, came a solution (or compromise).
May 16-- YES! (but not right away)
Started the day by finishing up the cut from Friday. Uh oh (view from below).
Time to grind this mess :(
Two hours of swearing and grinding, and swearing... still grinding...(and swearing)...
The problem is, with mild steel, oxygen is used to facilitate the cut-- and I think it's really
the major player in cutting-- not the laser beam.
It's harder to focus a jet of gas than a beam of light!
But, the stainless that we ordered early last week finally arrived, as did the tank of nitrogen. Now to see what happens without O2:
The twigs are ~1mm wide,the kerf if ~.02" and the
stainless is 6mm thick. This is what I want! (compare to May 11)
Some more tests, this time in 2mm thick material. The waviness is due to inertial effects from the table wobbling
after quick direction changes (not a problem, going slower, with thicker material).
May 13-- a better day:
The previous day's tip problems left us with some nasty areas of dross.
However, after a little time with the angle grinder, it's looking a whole lot better.
short clip of this thing being cut (1.21M wmv)
May 12-- another tough day:
ideally, the laser head hovers 1mm above the piece to be cut. Unfortunately,
the steel plate warps a bit when it gets hot...
...resulting in a badly damaged tip (replacement parts are in Pamplona-- several days to get.)
I am very bummed.
In very Basque-like tradition, Alfredo (shown here) and Juanma are not ready to quit. They figure out a way to machine the damaged tip...
...and we are back in business!
May 11-- tough day:
turns out to be not so simple to
get a clean, high-detail cut :(
there are *many* parameters to set, and get wrong
after 37 tries, we're getting closer...
May 10-- We are finally ready to begin cutting steel:
out with the welding head
in with the cutting head.
finding the best focal point by blasting holes in film
(.96M wmv)
and then it is time for our first cut:
"You expect me to talk, Goldfinger?"
"No Mr. Bond. I expect you to die!" (1.16
wmv)
May 5-6:
The CO2 laser.
250W (10% power) through the welding head.
first tests-- 100mmx100mm
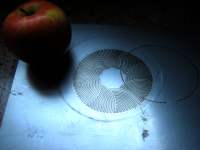